What is stocktaking?
Stocktaking (or stock counting) is when you manually count and record all the physical inventory and compare it to your systems reported quantity on hand. It’s a vital part of your inventory control and affects your purchasing, production, and sales departments.
Why are stocktakes important?
Performing a complete stocktake is essential to maintaining healthy inventory levels and account for any losses, not to mention keeping the accountants happy! Often forgotten is the level of impact inventory control has on a business’ cashflow. The key benefits to conducting regular stocktakes include:
- Determine the health of your inventory control processes: Relying entirely on your inventory management system for accurate levels is usually a bad idea. Stocktakes can identify discrepancies and poor inventory control before it becomes a major problem.
- Discover stock issues: Inventory management systems will enable you to track product levels and locations but cannot identify issues such as damaged products, missing products, poor location control or product theft.
- Ensure your business is meeting targets: Once you know exactly how your inventory control is performing you can refine your procedures and plans to increase stock efficiency and improve margins. For example you might reduce the amount of on hand safety stock or change up pricing to move stock.
What's the right approach to stocktaking?
Every business is different, and the process of stocktaking will vary hugely from company to company, however the best approach would always be to chunk your products groups down and perform cyclical stocktakes where possible.
Here are our essential tips for conducting a stocktake with maximum effectiveness!
1. Schedule
Trying to run a high volume count during business hours is not always feasible as it can interfere with day-to-day operations. Try to find a time that works for the business and your staff that will not impact on service delivery. Consider that you may need to stop trade to count and that you will need time set aside afterwards to resolve discrepancies and fix issues.
It is important to cut off all purchases and sales during the count. Otherwise, the incoming and outgoing stock will affect your count.
2. Tidy
A stock area which is clean and well organized will make it easier to find and count stock thereby reducing the possibility of miscounts. Well defined locations and labelled stock will make your stocktake process more efficient.
It's also a good idea to pre-count items into lots of 10, 50 and 100, when counting large quantities of individual stock items. Anything that you can do to tidy up your physical stock is useful and ensures mistakes may be avoided later on.
3. Organise
Before you begin the stocktake process make sure that the team have the tools they need to get the job done efficiently. Some of the resources you typically need to perform a stock count include:
- Mobile Devices if compatible with your inventory management system
- Handheld bar code scanners
- Laptop
- Clipboard
- Stock Count Sheets
- Pens
- Calculators
- Weight Scales
4. Communicate
Give your team clear timeframes and responsibilities. Your stocktake supervisor should have a list of what needs to be counted and stock takers should know what tools they need and how they are going to count the stock. If your stocktake is going to take some time to complete, ensure that the team have regular breaks to keep minds and eyes fresh to reduce mistakes.
5. Know what you’re counting & how
Whether you have a small stockroom with a few types of inventory or a large warehouse filled with a wide range of stock, it is essential you create a clear system and explain how you would like your stock to be counted.
- Ensure stock takers know which sections they will be counting and in what order.
- Have stock takers count in the same direction — i.e. left to right, top to bottom.
- Mark counted stock with a coloured pen / marker or sticker as a visual cue of what’s already been included in the stocktake.
Creating a similar process with methods that are clearly defined will ensure you are in the best position for a smooth well organised stocktake.
6. Timely Data
The goal of any stocktake is to get an accurate count of your on hand inventory. Generate stock count sheets from your inventory management system on the day of the count and prevent inventory transactions being processed between count generation and count completion. Most systems will allow you to create the count parameters, but not generate the snapshot until you are ready.
Stock that hasn’t shipped is essentially not yours anymore if it has been issued from your inventory so exclude items that have already been picked for delivery and or invoiced to customers but haven’t yet shipped. Raw materials that have arrived but haven’t yet been entered into your inventory system can also be excluded from the count.
7. Action the Count
Once the initial stocktake count is completed, you need to check for variances and conduct a recount if necessary. Variances can be under or over, both of which affect the valuation of the stock. If you have variances in your stock, you need to find out why. Some common reasons for variances in stock include:
- Items marked with an incorrect label
- Stock stored in multiple locations
- Dead stock not scrapped correctly
- Stock counted multiple times
- Stock put away but purchase receipt not yet processed
- Other stock transactions not yet approved / processed
Unaccounted stock variances will cost your business, hence the need to check each line for a potential reason why stock is out of balance. Materiality also plays a part here as small variances might be considered immaterial; however, consistently small variances of the same product become material and may point to a pattern of process failure or worse case, fraud.
8. Keep Prices Current
After the inventory has been counted, all variances have been considered and you are confident you have counted everything correctly, it is time to update the stock levels. This process often creates a financial transaction known as a stock count variance which is the side effect of the change in inventory valuation caused by any differences between the physical count and the quantity on hand reported by the inventory system.
For this reason, it is important to ensure that your Item prices remain current. Having outdated values can ultimately result in your inventory value being listed inaccurately and have a direct impact on your business profitability.
9. Evaluate
Stocktaking shouldn’t be a static process that follows a rigid set of procedures – it should evolve and change over time, that way the process can become more efficient. Your stock takers and supervisors should be encouraged to suggest improvements and help develop innovative procedures to produce a more effective workflow. An easy way of doing this is to provide opportunities for feedback at the end of your stocktake.
Technology can also help streamline the process and make it easier to track inventory throughout the year.
The Software team at Cutcher & Neale have extensive experience in business process consulting, training, software and technology that can improve your stocktake process. Contact our team if would like to review your stocktake process.
Bonus Tips & Shortcuts
- If an urgent order needs fulfilling during a stock count, ensure this is communicated to all and the change in stock is recorded Manually for adjustment of the count before its committed. Once committed, record the manual pick in your system.
- For inventory stored in bags or boxes don’t assume that internal contents are correct. Open and count the contents if practical to improve count accuracy. This can be done in the week leading up to the full stock count to improve efficiency but if doing so this must be clearly communicated to your entire team to ensure that contents are not inadvertently consumed.
- Pre count slower selling stock into easy multiples (10, 50, 100) during the week leading up to the full stock count to improve efficiency on stocktake day.
- Ensure your stock takers know the products. If Bob is counting your widgets but doesn’t know Widget A from Widget B, then the count result may be inaccurate.
- Chunk down your stocktake by using locations, categories, or suppliers to reduce the inventory count list. Make sure that you maintain a consistent method across the count so as not to double up on stock being counted or miss counting it at all.
- Consider a cyclical count cycle that occurs throughout the year so stock take becomes a regular part of your weekly stores process.
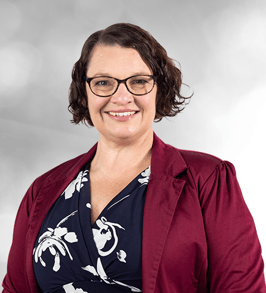
Cutcher's Investment Lens | 25 - 29 August 2025
First home vs investment property
Cutcher's Investment Lens | 18 - 22 August 2025
What doctors in their 30s, 40s & 50s should do with their investments
Cutcher's Investment Lens | 11 - 15 August 2025